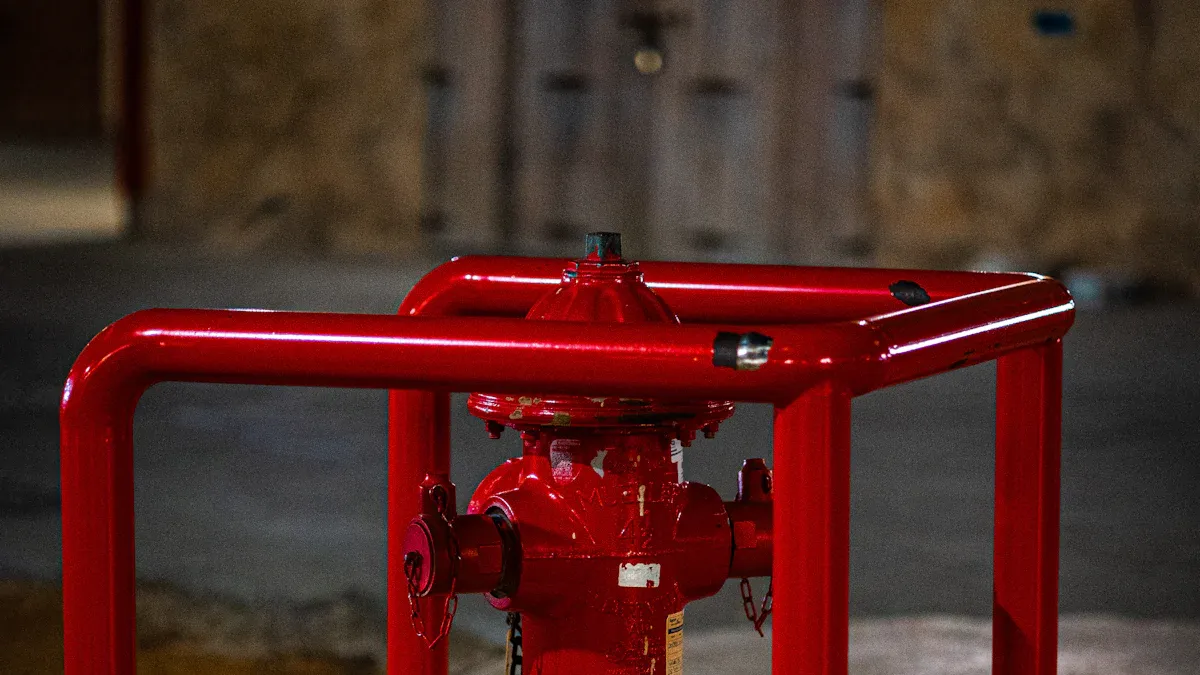
High Temperature Butterfly Valves help control how liquids and gases move. They do this by turning a disc inside the valve with a quick quarter-turn. These valves have strong metal seats and special designs. This helps them work in very hot places, sometimes up to 815°C, and under high pressure. They seal tightly and stop leaks even when temperatures change fast. This makes them very important in power plants, chemical factories, and other tough jobs.
Key Takeaways
- High temperature butterfly valves move hot liquids and gases. They do this by turning a disc inside with a quick turn.
- Strong metals like stainless steel make these valves safe. Special seals also help them work in very hot and high-pressure places.
- Double and triple offset designs help the valves last longer. These designs also make the seal better and reduce damage from heat.
- Many power plants and chemical factories use these valves. They need good flow control in hard conditions.
- Checking the valves often and taking care of them is important. This keeps them safe, stops leaks, and helps them last longer.
High Temperature Butterfly Valves
Definition
High Temperature Butterfly Valves help control hot liquids or gases in hard jobs. These valves have a round disc inside the valve body. The disc turns to start or stop the flow. The disc is attached to a stem. The stem connects to an actuator. The actuator can be manual, electric, or hydraulic. When the actuator moves, it turns the stem. This makes the disc turn and opens or closes the valve.
Industry rules like ASME A182 and ISO 10631:2021 tell how to make and test these valves. These rules say what materials, designs, and pressure ratings are needed. This keeps the valves safe in very hot places. Most High Temperature Butterfly Valves use strong metals like stainless steel or special alloys. These metals do not break down from heat or rust. This helps the valves last longer in tough places.
Note: High Temperature Butterfly Valves often use metal seats or special seals. These parts help the valve seal tight, even if the temperature changes fast.
How They Work
High Temperature Butterfly Valves work by turning a disc inside the valve. The disc turns a quarter turn to open or close the flow. If the disc is parallel to the flow, the valve is open. If the disc is turned across the flow, the valve is closed.
Here is a simple step-by-step process:
- The actuator pushes or pulls the stem.
- The stem turns the disc inside the valve.
- The disc moves from open to closed position.
- The valve starts, stops, or controls the flow of hot gas or liquid.
There are different types of butterfly valves for high heat:
- Zero-offset (concentric): The disc sits in the middle and seals with a soft seat. These work up to 400°F.
- Double offset: The disc and stem are set off twice, which lowers wear and lets them handle up to 1200°F.
- Triple offset: These have a third offset and use a special cam action. The metal-to-metal seal only touches at the very end. This design works best for very high heat and pressure.
A market study shows more industries use High Temperature Butterfly Valves now. This is because of better materials and smart monitoring. These changes help the valves last longer and work better in power plants, chemical factories, and other hot places. Engineering tests show these valves keep working well after many times opening and closing in hot, high-pressure jobs. Tests prove the valves stay safe and reliable, even after years of use.
Components
Disc and Body
The disc and body are the main parts of this valve. The disc sits inside the body and turns to control flow. These parts use strong metals to handle heat and pressure. For example, the Apollo Class 600 Carbon Steel Butterfly Valve uses a stainless steel disc. Its body is made from carbon steel. These metals do not get damaged by heat or rust. This helps the valve last longer in hard places.
The table below lists common materials for the disc and body:
Component | Material Description | Material Standard |
Body | Cast Steel | A216 Grade WCB/SCPH2 |
Disc | Stainless Steel | A351 Grade CF8M/SCS14A+HCr(3) |
Valve bodies come in different shapes like wafer, lug, or flanged. These shapes help the valve fit many pipe systems. The disc is often shaped to let fluids move easily. This shape also helps lower pressure loss. Some discs have a hard layer to stop damage from heat.
Manufacturers use drawings to show how the parts fit together. They use 3D models and 2D views to help engineers check the design. These tools make sure the valve will work well in real jobs.
Stem and Actuator
The stem links the disc to the actuator. The stem must stay strong and straight in high heat and pressure. Many makers use 17-4 PH stainless steel for the stem. This metal stays strong when it gets hot. It does not bend or break easily.
The actuator moves the stem and turns the disc. Actuators can be manual, electric, pneumatic, or hydraulic. Some valves use ISO 5211 mounting flanges. These flanges make it easy to add different actuators. The Fisher 8532 High Performance Butterfly Valve can use many actuator types. It uses splined shaft connections for a tight fit.
Tip: Picking the right actuator helps the valve work well and safely in hot jobs.
Makers add safety parts to the stem and actuator. These can be anti-blowout glands and pressure seals. These parts keep the valve safe and working, even after years in tough places.
Design Features
Materials
Engineers pick special materials for high temperature butterfly valves. These materials can handle very hot and harsh places. Metals like stainless steel and super duplex stainless steel do not rust. They stay strong even when it gets really hot. Some valves use PTFE or lined pfa F46 to fight strong chemicals. Material test reports and charts help engineers choose the best material for each job. The table below lists common materials, their heat ranges, and where they are used:
Material | Temperature Range | Chemical Resistance Highlights | Typical Applications |
Viton | -20°C to 200°C | Excellent resistance to acids, fuels, oils, solvents | Chemical plants, water systems, seals |
Lined pfa F46 | -200°C to 260°C | Excellent resistance to strong acids, alkalis, solvents | Chemical processing, pharmaceutical manufacturing |
PTFE | -200°C to 260°C | Excellent chemical resistance, smooth surface | Chemical plants, high temperature systems |
Stainless Steel | -100°C to 500°C | Good resistance to oxidizing acids and solvents | High-pressure industrial systems |
Super Duplex Stainless Steel | -50°C to 300°C | Superior corrosion resistance, especially in seawater | Oil and gas, heavy-duty applications |
EPDM | -40°C to 120°C | Good resistance to diluted acids and alkalis | Water treatment, steam systems |
PVC | 0°C to 60°C | Moderate resistance, limited temperature | Low-temperature water systems |
CPVC | Up to 93°C | Better chemical and temperature resistance than PVC | Hotter chemical systems |
Safety rules and certificates help make sure these materials work well. Engineers use computers to test how materials act under heat and pressure. These tests help them pick the right material for each valve.
Sealing Mechanisms
Sealing mechanisms stop leaks, even when it is very hot or under high pressure. Many high temperature butterfly valves use metal seats or graphite rings. These seals last longer than soft ones and seal tightly. Some valves use composite seals with both hard and soft parts for extra safety.
- Graphite rings work well up to 350°C and high pressure.
- Special coatings like FeAl intermetallics protect at 650°C and lower wear.
- Triple offset designs use a cone-shaped seat to stop leaks during pressure spikes.
- Testing rigs copy real heat and pressure to check how well seals work.
- Composite seals with graphite and PTFE are good for tough, hot jobs.
Engineers test seals to make sure they last a long time. These tests show that good seal designs stop leaks, even after years of use.
Double Offset Design
The double offset design helps these valves work better in tough places. In this design, the disc and stem are set off-center in two ways. This makes less friction and wear when the valve moves. The disc leaves the seat fast, so the seal only touches at the end. This helps stop damage and makes the valve last longer.
Computer tests and real-life tests show double offset valves handle heat and pressure well. Shock tests, like those used in navy ships, show the valve stays strong under sudden force. Engineers use tools like ANSYS to see how the valve handles stress and heat changes. These tests prove the double offset design seals better, wears less, and keeps the valve safe in hot jobs.
Applications
Power Generation
Power plants use High Temperature Butterfly Valves to control steam, water, and gas. These valves keep things working well, even when it gets hotter than 200°C. Workers use them in both old and new energy plants, like geothermal and solar. The valves help move heat fluids and cooling water. This helps save energy and reach green goals. Their small size saves space, which is good in crowded power plants.
- The quarter-turn action needs little force, so the valves are easy to use.
- Tight seals stop leaks, which makes things safer and more efficient.
- Low pressure drop lets lots of fluid move fast, so plants work better.
- The valves can use manual, pneumatic, or electric actuators, so they fit into automatic systems.
Chemical Industry
Chemical plants use these valves to control liquids and gases quickly and safely. Their small size fits big pipes, and the quarter-turn lets workers shut them fast or control flow well. Lined butterfly valves with PTFE or rubber protect from strong chemicals. Metal-seated valves handle high pressure and heat, which is common in chemical jobs.
Aspect | Summary |
Valve Type | High-performance valves for pressure and temperature control in chemical processing. |
Material | Stainless steel and alloys resist corrosion and provide strength. |
Design | Double and triple offset designs ensure tight sealing and low leakage. |
Application | Used in large pipelines for fast operation and compact installation. |
Lined Valves | PTFE or rubber linings protect against acids and caustics. |
In 2024, these valves made up more than half of the European market money, showing they are very important in chemical plants.
Other Uses
Many industries use these valves. Renewable energy plants use them for moving heat fluids. Food and drink factories pick clean designs for milk, juice, and soda. Shipbuilders put them in ships for ballast water and engine cooling. Powder engineering uses them to control powders in cement and mining. Flue ventilation systems use them for air and hot gas. Oil and gas companies use them for pipelines and emergency stops. Water treatment plants need valves that do not rust for safe work.
Industry Sector | Application Example | Key Feature |
Food & Beverage | Liquid handling, quick cleaning | Hygienic design, tight seals |
Marine | Ballast water, engine cooling | Rust resistance, lightweight |
Oil & Gas | Pipeline flow, shutdown systems | High pressure and heat resistance |
Water Treatment | Flow control, isolation | Corrosion-resistant materials |
Note: High Temperature Butterfly Valves are useful in many fields, showing they work well in both tough and clean places.
Performance Requirements
Temperature Range
High Temperature Butterfly Valves must work in very hot places. Many valves can handle heat up to 400°C (752°F) if they have metal seats. Some special valves can work in even hotter spots, up to 815°C (1500°F). The materials used for the body and seat decide how hot the valve can get. Stainless steel parts are safe up to 800°F. Carbon steel cannot go as high. When it gets hotter, the pressure rating goes down. Engineers use charts to help them pick the right valve for the job.
Material/Component | Temperature Range (°F) | Pressure Rating (psi) | Notes |
Carbon Steel | -20 to 400 | See ASME B16.34 | Pressure drops as temperature increases |
316 Stainless Steel | -50 to 800 | See ASME B16.34 | Good for higher temperatures |
Duplex/Alloy Steels | Higher than 800 | See ASME B16.34 | For severe conditions |
EPDM (Seat/Seal) | -20 to 250 | Up to 150 | Lower temperature use |
Viton® (FKM) | -10 to 400 | Up to 150 | Good for higher temp seals |
PTFE | -100 to 450 | Up to 300 | High temp and pressure resistance |
Makers say you should pick a valve that can handle more heat than you expect. This helps stop damage.
Durability
Valves need to last a long time in tough places. Engineers test them in labs to see how they hold up. They use tests like the Thin Film Oven Test. These tests show if seals and metals can take the heat and pressure. Metal seats and strong alloys help the valve last longer. Good valves keep leaks away after thousands of uses. If the valve is built well, quick changes in heat or pressure will not make it leak.
- Metal seats last longer than soft seats.
- Composite seals with PTFE or graphite help valves last longer.
- Valves must work in steady heat and sudden heat spikes.
A strong valve means factories do not have to stop work often. This saves money on repairs.
Standards
Industry rules help keep these valves safe and working well. ASME B16.34 gives the main rules for pressure and heat. API 609, API 598, and API 6D tell how to design, test, and check the valves. These rules say valves must pass tests for holding pressure, sealing, and opening and closing many times.
- API 6D: Rules for pipeline valve design and testing.
- API 598: Rules for checking and pressure testing.
- API 609: Rules for butterfly valve design and rating.
- ASME B16.34: Rules for pressure and heat limits.
- ASME B31.1 and B31.3: Rules for piping system safety.
Valves that follow these rules pass hard tests for strength and safety. Factories trust these valves for tough jobs.
High temperature butterfly valves have a disc that turns to control flow. They work well in hot and tough places. Some have double or triple offset designs. These designs help them last longer and seal better. Strong metals like stainless steel make them tough. The valves open and close fast. They let you control how much liquid or gas moves. Using these valves can save money. Engineers must look at the size and pressure rating. They should also check if the material fits the job. The way the valve opens, and the type of seal, are important too. This helps pick the right valve for the system.
FAQ
What makes a butterfly valve suitable for high temperatures?
Engineers pick strong metals like stainless steel or special alloys. These metals do not get weak from heat or rust. Metal seats and special seals help stop leaks. They keep the valve tight, even if the temperature changes fast.
How often should high temperature butterfly valves get inspected?
Most factories look at these valves every six months. Checking them often helps find damage, leaks, or worn parts early. This keeps everything safe and working right.
Can high temperature butterfly valves handle both liquids and gases?
Yes, these valves can control hot liquids and gases. Power plants and chemical factories use them for steam, water, air, and other fluids.
What is the difference between double and triple offset butterfly valves?
Double offset valves have two offsets to lower wear and seal better. Triple offset valves add a third offset and use a cone-shaped seat. This makes the seal tighter and helps the valve last longer.
Do high temperature butterfly valves need special maintenance?
Tip: Only use cleaning agents and lubricants that are approved.
Workers should follow the maker’s guide for care. They need to check seals, seats, and moving parts. Good care helps the valve work safely and last longer.